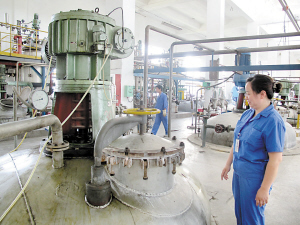 | 设备初步安装到位。 |
|
■ 项目名称:洛阳鸿安生化科技有限公司“固定化酶法”D-对羟基苯甘氨酸高技术产业化生产线
■ 开工时间:2009年
■ 竣工时间:2010年夏
■ 项目概算投资:1.23亿元
■ 目前进度:厂房竣工,设备初步安装到位,已具备生产条件
D-对羟基苯甘氨酸是什么东西?一种状如盐粒的白色晶体,广谱抗生素消炎药的重要成分之一。我们日常生活中常见的阿莫西林、头孢氨苄等消炎药品,都含有这种物质。
“我们公司新引进的‘固定化酶法’生产方法是最先进的,此前国外只有一家企业采用此法进行生产,国内一家也没有。”说这话的是洛阳鸿安生化科技有限公司(以下简称“鸿安生化公司”)工作人员余菲。上周,记者随余菲来到鸿安生化公司,发掘“新”字之后的奥秘。
玉米浆发酵很环保
鸿安生化公司位于洛阳工业园区小浪底专线旁,厂区不大。新厂房有两栋(其中一栋是在旧厂房基础上扩建的),总面积约4000平方米。厂房里面竖着一个个大锅炉似的铁皮罐子,还有一些怪模怪样的机器。机器的噪声很小,几名穿蓝衣的工人走来走去,观察着仪表盘。
厂房外摊放着几堆灰黄的渣滓,闻起来有酸味。工作人员说,那是发酵后的玉米浆。
据余菲介绍,早年,鸿安生化公司用的是化学拆分法生产方式,从化学原料中提取所需物质,工艺简单,但生产过程中会生成有害物质,造成药品有害成分残留,副作用大。后来该公司改进技术,采用较传统的“一菌两酶”生物法生产方式:把菌种放到玉米浆里发酵,生成酶,再转化提取D-对羟基苯甘氨酸。所用原料都是微生物,绿色环保。
曾受日本企业打压
“一菌两酶”生产法虽然环保,但是也有弊端:酶是一种微生物,一经使用,活跃度会降低,不能重复利用。为了持续生产,需要不断追加原料投入;再者,生产过程中耗水量大,废水排放量也大。生产成本高,产能上不去,利润空间自然就小。
余菲讲了一个例子:金融危机前,每吨D-对羟基苯甘氨酸的市场售价是8万元,后来日本企业以每吨6万元的售价向中国市场倾销D-对羟基苯甘氨酸,“因为人家有新技术,生产成本低,敢压价”。这使得以鸿安生化公司为代表的一批国内相关企业举步维艰。
“次抛型”
变“耐用型”
2009年7月,鸿安生化公司与中国科学院上海生命研究院湖州工业生物技术中心合作,引进世界先进技术——“固定化酶法”D-对羟基苯甘氨酸生产法,依托高新技术,修炼企业内功。
“固定化酶法”与传统生物法最大的区别,在于前者产出的酶可以重复利用。“这里面的工艺比较复杂,简单来说,我们将酶固定在一个载体上,使它可以多次使用,利用率成百倍提高。”余菲解释说。
这好比士兵上阵,有了载体的酶,就像全副武装的战士,自然比手无寸铁的杀伤力强许多。
由于配套设备尚未全部安装到位,鸿安生化公司只是小规模试运行新技术生产方式,“大概还需要1个月左右,产能才能全部释放”。余菲说:“新的生产方式,不但节省了劳动力、降低了劳动强度,而且大大提高了产能:原来生产一批成品需要30多个小时,采用新技术后,14个小时就能生产50多批;原来年产量不到500吨,以后能提高到3500吨。”